Industrial CT Scanning of Cracks & Fractures
Industrial CT for Cracks & Fractures
Some benefits of additive manufacturing are the fast iterations coupled with the levels of complexity that can be produced in a single component. Inaccessible, internal geometry can reduce the number of parts required, and offer engineers a way to completely redesign a traditional part. However, inspection of these inaccessible geometries can be difficult. Some choose to section the samples for inspection with traditional methods, while others rely on Industrial CT Scanning to create a electronically tactile 3d twin of the part for analysis, inspection, FEA, and more.
This case study demonstrates the ability to locate and image cracks and fractures ranging from 3 inches to 10 microns.
Two Industrial CT Methods
This sliding comparison shows two methods of CT inspection – helical scanning and focus scanning. Helical scanning allows us to acquire the highest resolution for oblong parts.
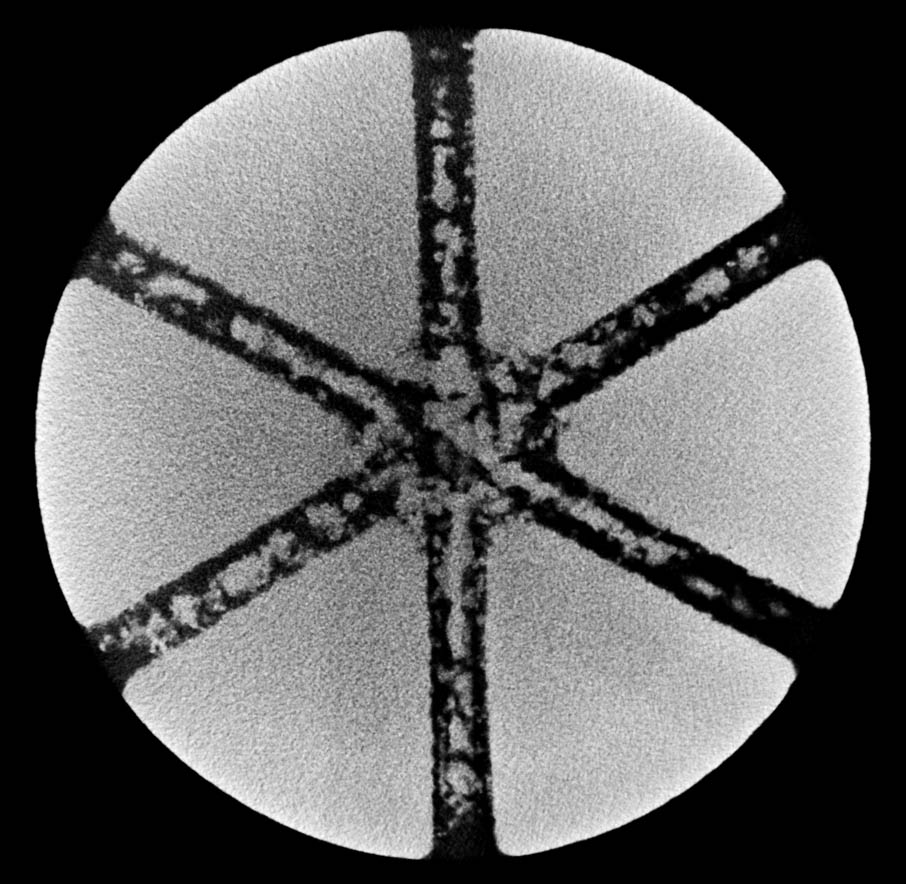
Helical – This dataset is lower resolution (22um) but captures the entire 8.5 inches of the part totaling 96gb.
Focus, Circular – This data set is the highest resolution possible for this part (4um), but only about .27 inches tall and 12gb.
Each method has their pros and cons. Helical is great for high resolution, general inspection, but at the loss of quality. Focus circular is great for maximum quality but a very small inspection region.
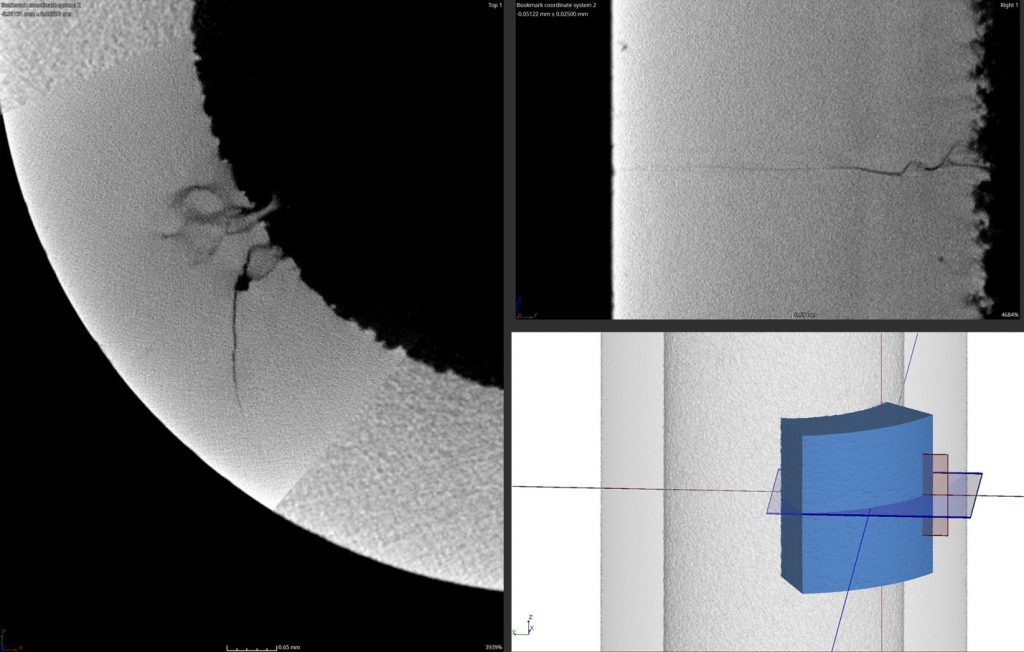
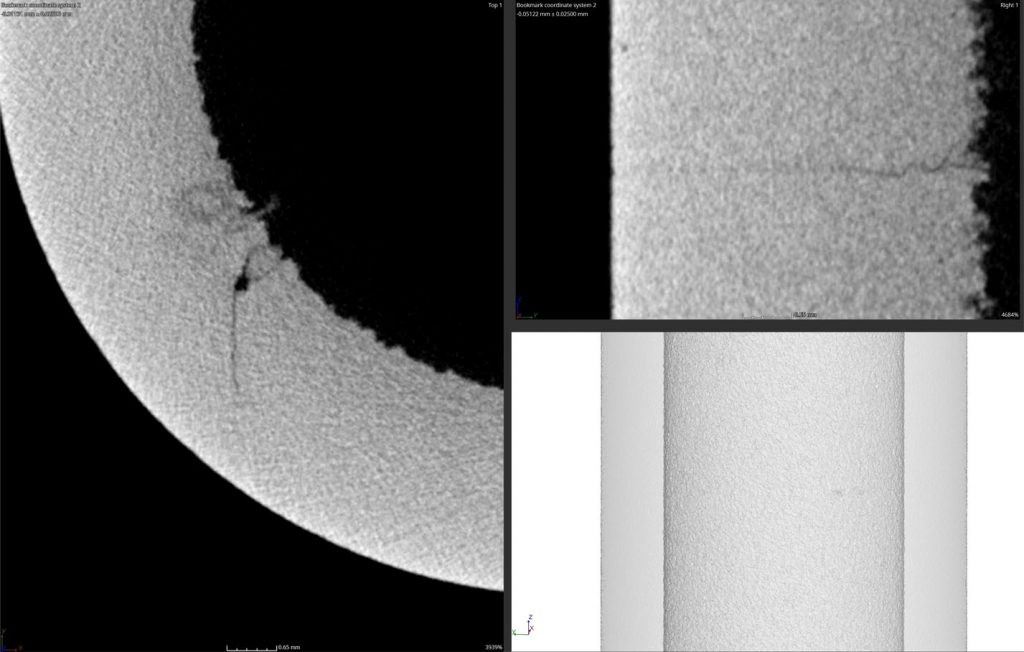
Here is a side by side of each method demonstrating the quality difference. While the helical scan’s quality is noticeably lower, the entire part is captured. It would not be feasible to capture the entire part using focus circular because of how many datasets would be required. Helical should be used for the general inspection, and focus circular for further investigation.
Surface Level Cracks
Some cracks are surface breaking. Clients use CT to understand point of origin, severity, travel, and underlying material conditions. Was there porosity or shrink? Was material thickness low?
The crack to the right is 3 inches in length.
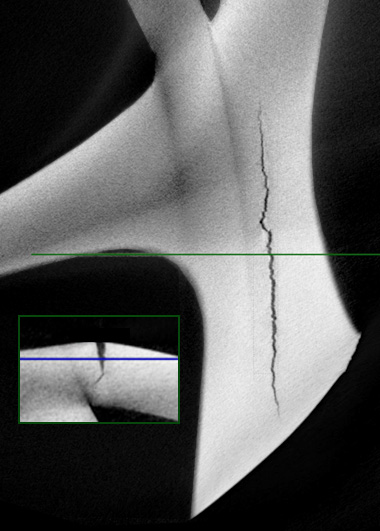
Component Failure Investigation
Some cracks are only found after failures in the field. The crack is so small that we need to perform an investigation to locate it. The part was filled with fluids making other forms of non-destructive testing more challenging.
This example crack is just 10um in width and nearly impossible to see visually.
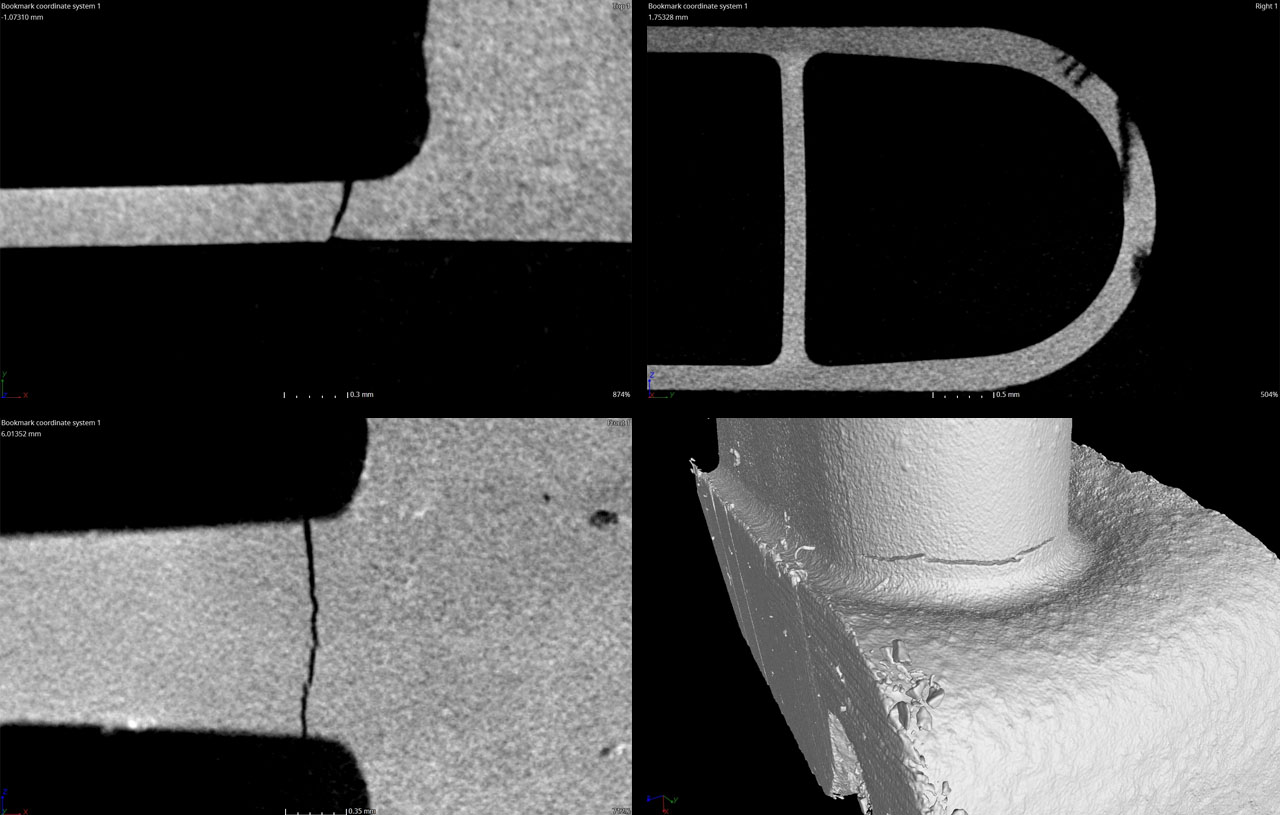